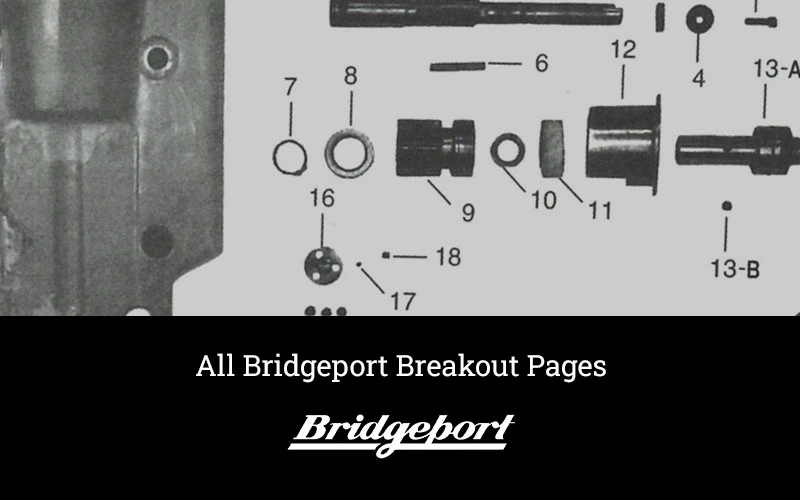
The functionality of complex machinery relies heavily on the intricate arrangement of its various components. A comprehensive understanding of these elements is essential for efficient operation and maintenance. This section will provide valuable insights into the configuration of a specific machine, enabling users to visualize and identify critical parts.
By exploring the layout and interconnections of these individual elements, operators can enhance their proficiency in managing the equipment. Detailed representations serve as invaluable tools for both novice and experienced users, ensuring that everyone can navigate the intricacies of the machinery effectively.
In the following sections, we will delve into the specific characteristics and roles of each component, illustrating their significance in the overall functionality of the device. This knowledge is crucial for troubleshooting and performing necessary adjustments to maintain optimal performance.
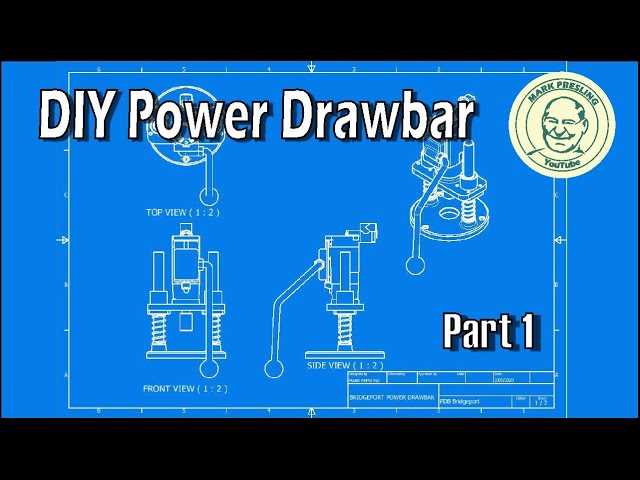
The machine is built from several vital elements, each contributing to its overall functionality and precision. Understanding these core elements is essential for ensuring efficient operation and maintenance.
Spindle Assembly: The spindle plays a crucial role in the machine’s functionality, being the part that rotates the tool. Its speed and power are critical for the success of any task, making it one of the most important elements to monitor.
Table: The flat surface where materials are placed during the operation. The table is adjustable, allowing for precise positioning and securing of materials, which is essential for accurate machining processes.
Knee: This component is responsible for supporting the table. It provides the necessary vertical movement, allowing the table to be adjusted in height, enabling fine-tuned control over the machining process.
Understanding the Parts Diagram
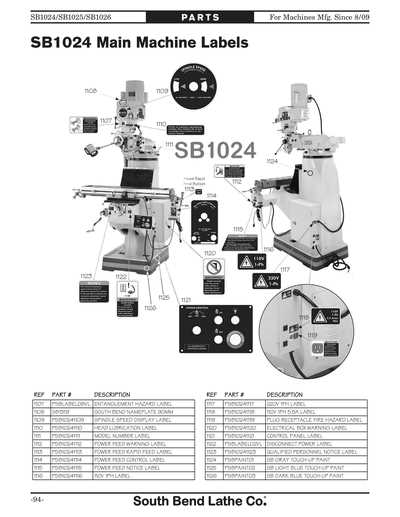
When dealing with complex machinery, it’s crucial to have a clear representation of its components and their relationships. These detailed illustrations serve as a visual guide, providing insights into the structure and function of each element. By examining these schematics, one can better understand the positioning and interaction between the different sections, which is essential for both maintenance and repairs.
Key Components Overview

Each component plays a distinct role in the overall operation of the machine. The layout helps users identify crucial sections that may require attention. Understanding how these elements connect is vital for efficient problem-solving and upkeep.
How to Use the Diagram
To navigate the schematic effectively, it’s helpful to break down the machine into smaller sections. Each section is labeled to correspond with the relevant component, making it easier to locate and address specific issues as they arise.
Identifying Major Assembly Sections
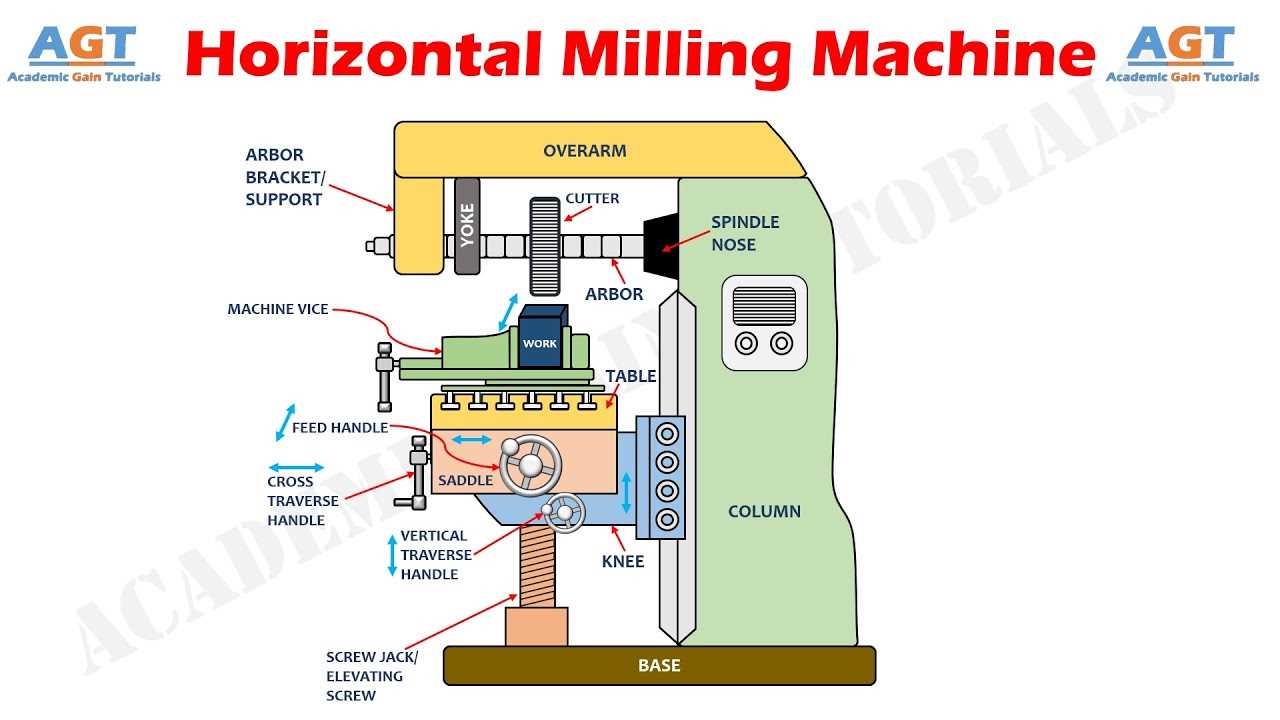
Understanding the main structural components of a machine is crucial for efficient maintenance and repairs. Each system is typically divided into several key sections, each playing a distinct role in the overall functionality of the equipment.
Base and Column Section
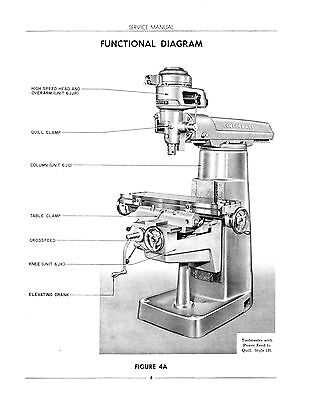
The foundation of the machine supports all other elements and provides stability during operation. This section often includes vertical and horizontal supports, ensuring the correct alignment of the moving parts.
Moving Components
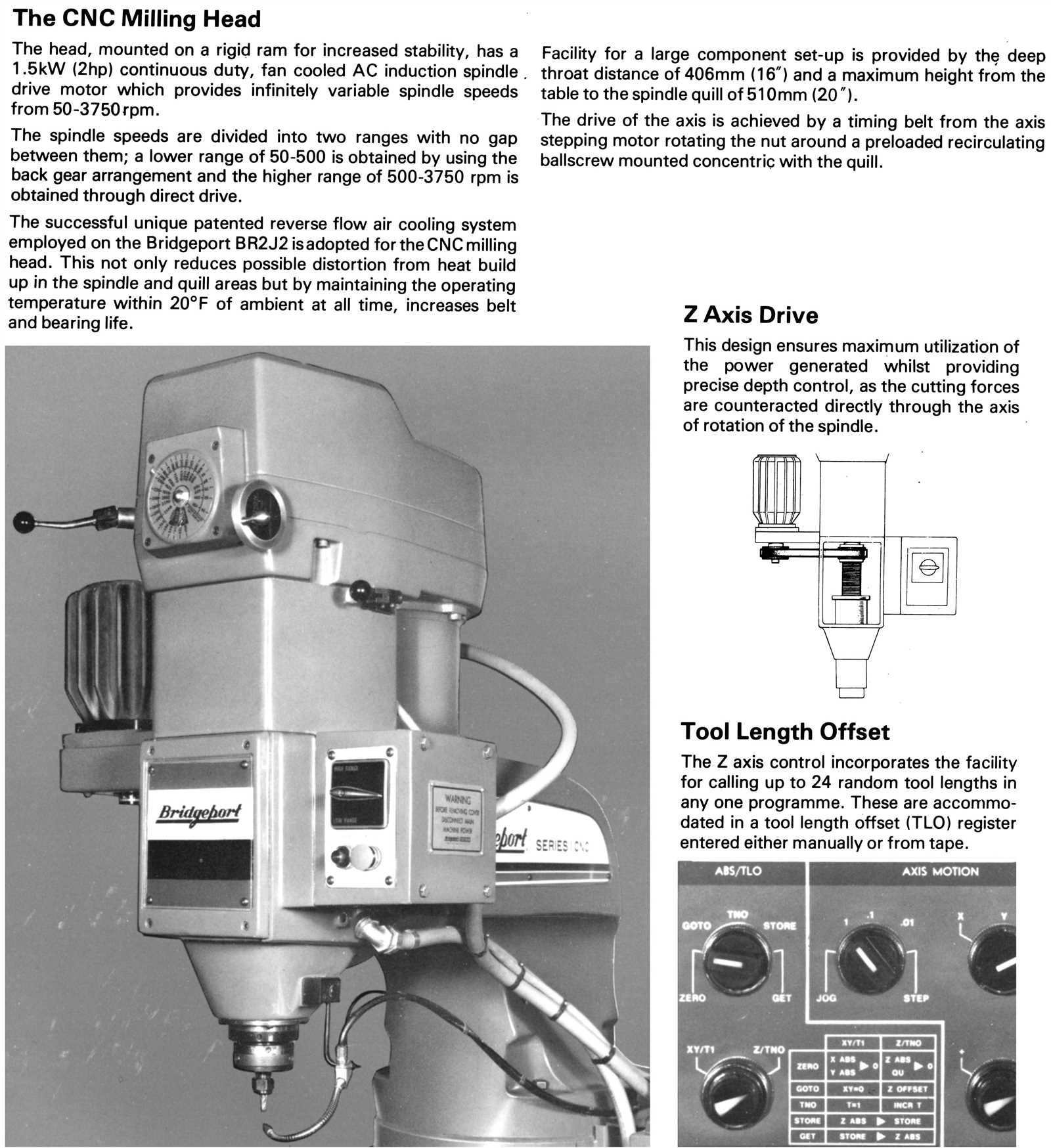
Another important section involves the elements responsible for movement, such as the mechanisms controlling vertical and horizontal motion. These parts ensure precision and accuracy in various tasks, allowing smooth operation.
Common Wear Parts and Their Functions
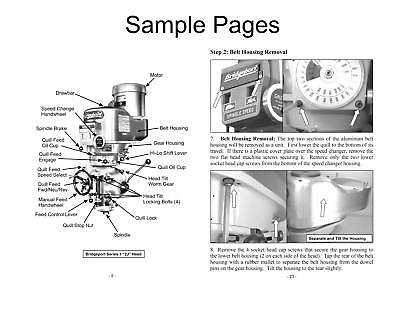
Over time, various components of milling machines are subject to wear and require replacement to maintain optimal performance. Understanding these frequently worn elements and their roles can help prevent breakdowns and improve the longevity of the equipment.
Bearings
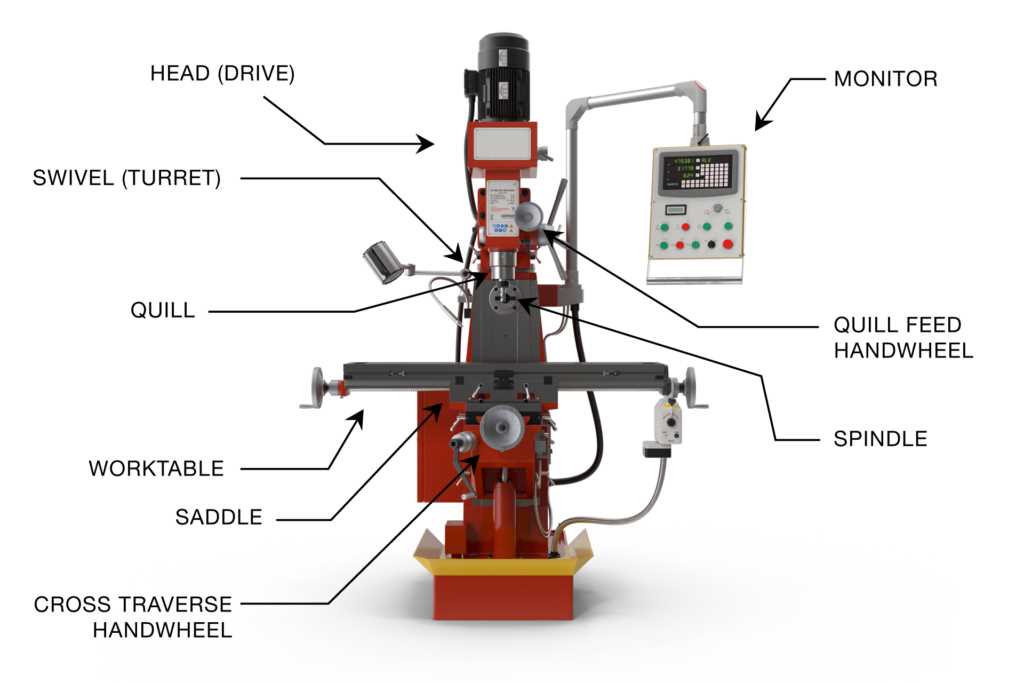
Bearings are essential for smooth rotational movement and reducing friction between moving parts. When worn, they can cause increased vibrations and reduce the accuracy of machining operations, leading to potential damage to other components.
Belts
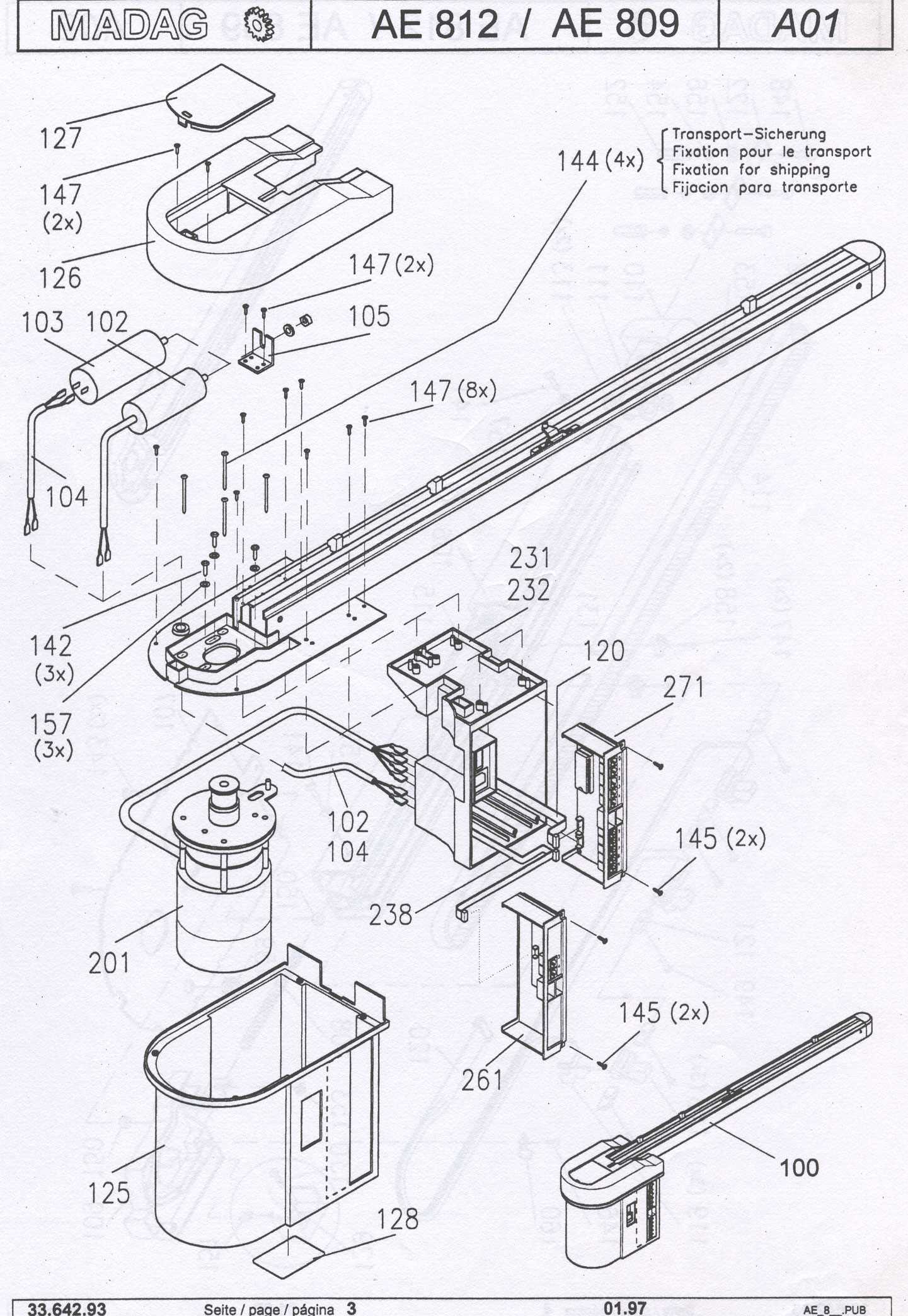
Belts transfer power from the motor to the machine, ensuring that it operates at the desired speed. Over time, belts may stretch or wear out, causing slippage or even failure, which reduces the machine’s efficiency.
- Timing belts: Critical for maintaining the synchronization between
Maintenance Tips for Essential Parts
Regular upkeep is crucial for ensuring the longevity and efficiency of any machinery. Focusing on critical components helps prevent unexpected breakdowns and ensures smooth operation over time. Understanding how to properly care for these key elements will help you avoid costly repairs and downtime.
Lubrication: Ensure all moving elements are well-lubricated to minimize friction and wear. This will reduce heat buildup and prolong the lifespan of the components. Regularly check and top off lubrication levels to maintain optimal performance.
Alignment Checks: Periodic inspections for proper alignment are essential to avoid excessive strain on individual elements. Misalignment can lead to uneven wear and mechanical issues that may affect the overall functionality of the system.
Cleaning
Replacement Parts Availability
Ensuring access to necessary components for machinery maintenance is essential to keep equipment running efficiently. Having a reliable source for replacement items extends the operational life of devices and minimizes downtime during repairs. This section discusses how you can find suitable alternatives when original components are no longer an option.
Commonly Available Components
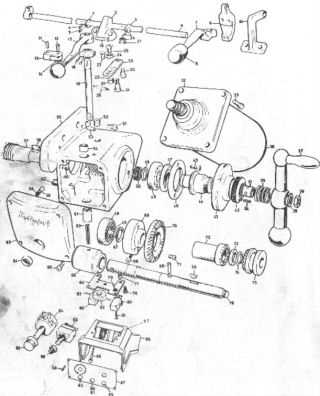
A wide range of essential mechanical and electronic elements are frequently stocked by specialized vendors. These items are designed to match various models, ensuring compatibility and ease of installation.
Sources for Hard-to-Find Elements
In some cases, older or specialized machinery may require unique pieces that are no longer mass-produced. For these, dedicated suppliers or custom fabrication options are often
Tools Required for Disassembly
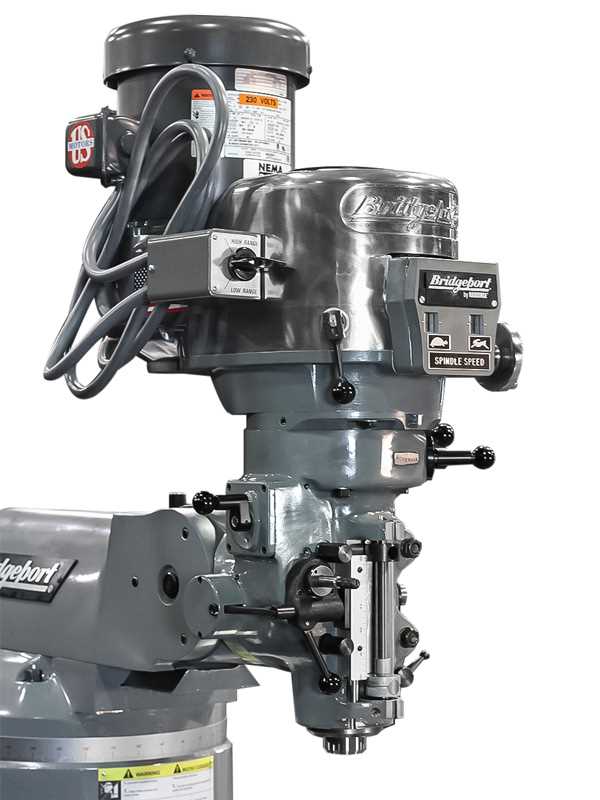
When preparing to take apart a machine, having the right tools is essential to ensure a smooth and efficient process. Using appropriate instruments helps avoid damage to components and speeds up the procedure.
Wrenches of various sizes are often necessary to loosen and remove bolts and fasteners. Make sure to use the correct size to prevent rounding off the heads.
A set of screwdrivers, both flathead and Phillips, is indispensable for accessing parts secured with screws. Choose the right tip to avoid stripping screws.
You might also need pliers or adjustable spanners for grip and turning tasks, particularly in tight spaces. Additionally, rubber mallets are useful when applying light force without damaging surfaces.
Finally, consider using hex keys
Step-by-Step Disassembly Guide
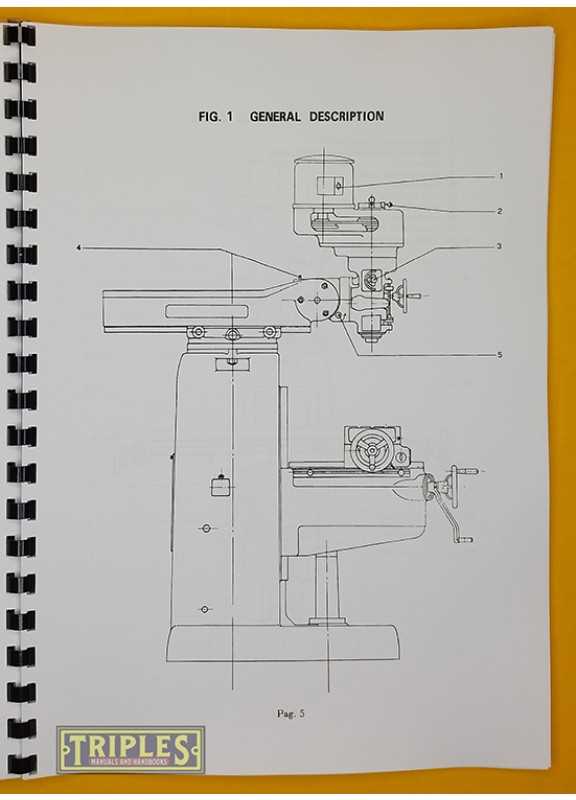
Disassembling a complex machine can be a challenging task, but following a clear and structured guide can make the process much easier. In this section, we will walk you through each stage of taking apart the equipment, ensuring you understand the key points at every step. Careful handling of each component is crucial to avoid any potential damage and ensure smooth reassembly later.
1. Preparation and Tools
Before starting the disassembly, gather all necessary tools and protective equipment. It’s important to have the correct tools to avoid damaging any sensitive components. Organize the work area to keep all removed parts in order, ensuring they can be easily identified for reassembly.
2. Initial Dismantling Steps
Begin by loosening the outer screws or fasteners that hold the main frame together. Gradually remove the exterior panels, paying attention to hidden screws or clips that
Common Issues and Troubleshooting
When dealing with equipment, it is crucial to recognize recurring problems that may arise over time. Understanding these frequent issues and knowing how to address them can help maintain the functionality of the machinery and prevent further complications.
- Inconsistent Performance: This can happen due to improper maintenance or wear of internal components. Regular checks and timely replacements are recommended to ensure smooth operation.
- Unusual Noises: Odd sounds during operation might indicate a need for lubrication or part alignment adjustments. Investigating the source can prevent significant damage.
- Overheating: Extended use or blocked ventilation can cause overheating. Ensuring proper cooling and airflow is essential for long-term use.
- Electrical Issues: Problems like flickering power or intermittent shutdowns could be due to faulty wiring or connections. It’s important to inspect and repair any electrical components promptly.
By staying vigilant and addressing these common challenges, users can extend the lifespan of their
Upgrading Parts for Improved Performance
Enhancing machine components can significantly improve its overall efficiency and extend its lifespan. By selecting modernized elements, operators can achieve smoother operations, reduce downtime, and optimize precision, resulting in better output quality. It is essential to consider not only the compatibility of new components but also how they interact with the entire system.
Key Components to Upgrade
Certain mechanical elements are particularly beneficial to upgrade for performance
Resources for Further Reading
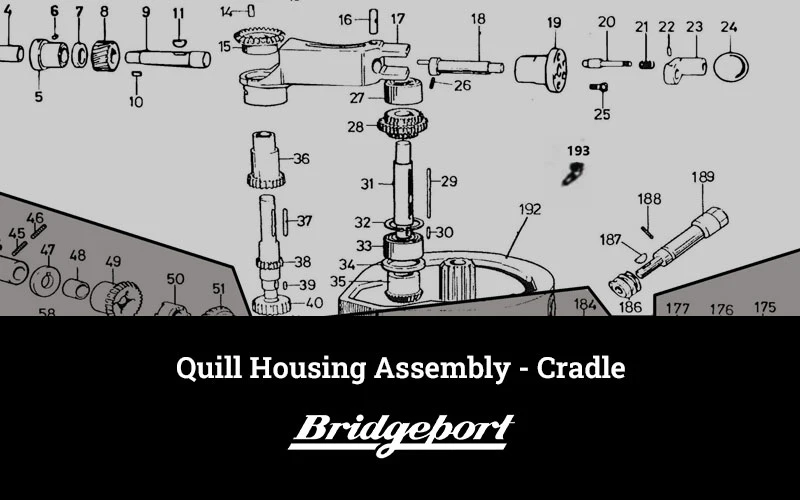
For those seeking to enhance their understanding of machining tools and their components, a variety of informative resources are available. These materials can provide valuable insights into maintenance, operation, and troubleshooting of equipment, helping users to optimize performance and longevity.
Books and Manuals
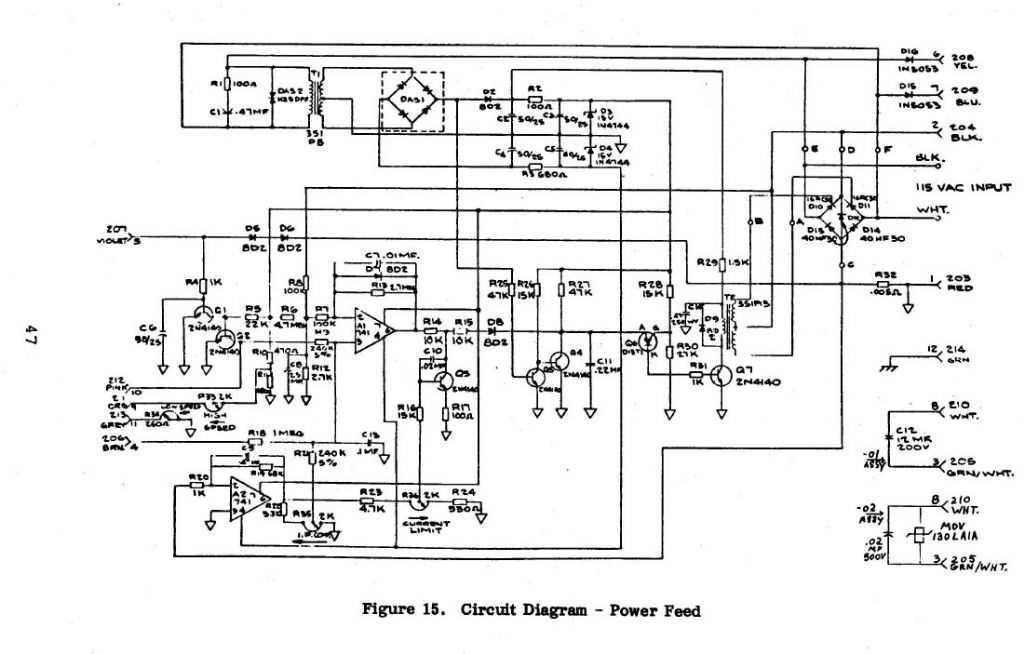
Technical literature offers in-depth knowledge and can serve as a valuable reference for both beginners and experienced users. Consider exploring comprehensive guides that cover fundamental principles, advanced techniques, and specific maintenance practices.
Online Forums and Communities
Participating in online forums can foster connections with other enthusiasts and professionals. Engaging in discussions and sharing experiences can lead to practical advice and solutions that may not be found in traditional publications. Websites dedicated to machining often have sections where users can ask questions and receive feedback from the community.