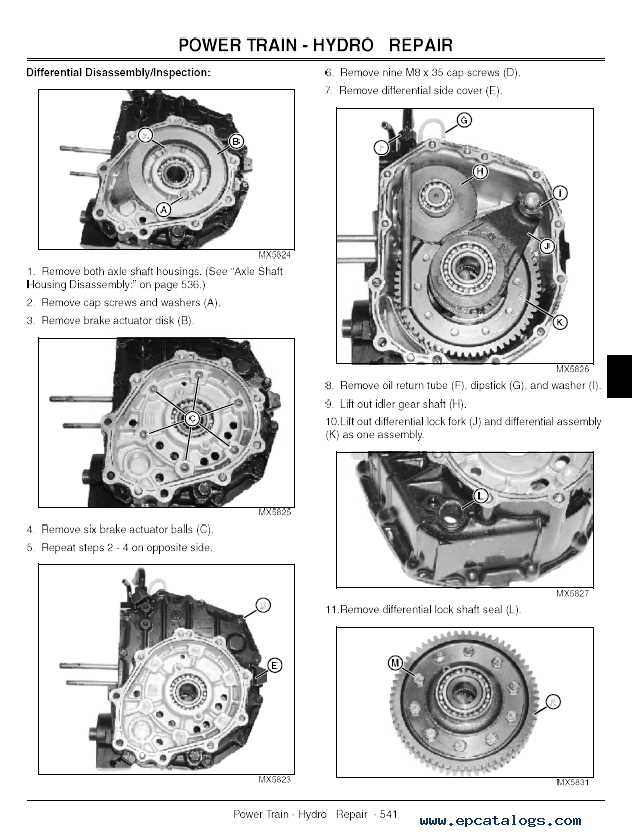
Understanding the structure and configuration of essential components is key to maintaining efficient operation of professional mowing equipment. When managing repairs or replacements, a clear representation of how each element fits within the overall system is invaluable. This guide provides insights into the essential elements that make up a reliable grass-cutting machine, ensuring smooth performance and extended durability.
The detailed breakdown focuses on the vital components involved in the cutting mechanism. Through visual representations and clear explanations, users will gain the knowledge needed to troubleshoot and maintain their equipment effectively. Whether for routine checks or specific part replacements, this resource helps ensure long-term efficiency.
Overview of John Deere 1435 Components
The machinery in question is composed of multiple critical elements that work in harmony to ensure efficient operation. Each segment plays a specific role in supporting the overall functionality, from movement to precision control. Understanding the placement and purpose of these sections is key to maintaining optimal performance and ensuring the longevity of the equipment.
Primary Structural Elements
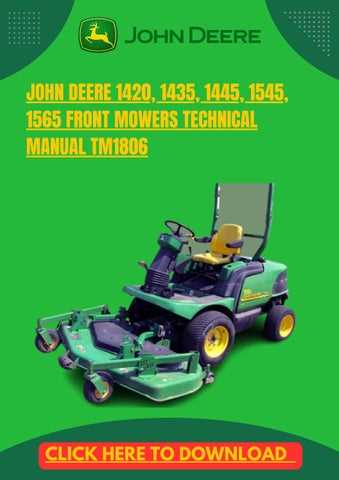
At the core of the equipment, robust structural elements form the foundation. These components are designed to withstand substantial wear while providing a stable base for the entire mechanism. Their durability is essential for supporting both the weight and the function of other interconnected systems, ensuring smooth operation in demanding environments.
Functional and Control Mechanisms
The
Key Features of the Mowing Deck
The cutting platform is an essential component that influences the efficiency and quality of lawn care. It ensures smooth grass trimming while offering flexibility for different terrain types. The structure of this unit combines durability and precision, enabling long-lasting performance and clean cuts, even in challenging conditions.
Durability and Build
One of the standout aspects of this cutting mechanism is its robust construction. Designed to endure tough environments, the materials used in its fabrication are resistant to wear and corrosion. This resilience allows for extended usage with minimal need for repairs, ensuring consistent functionality over time.
Adjustability and Cutting Precision
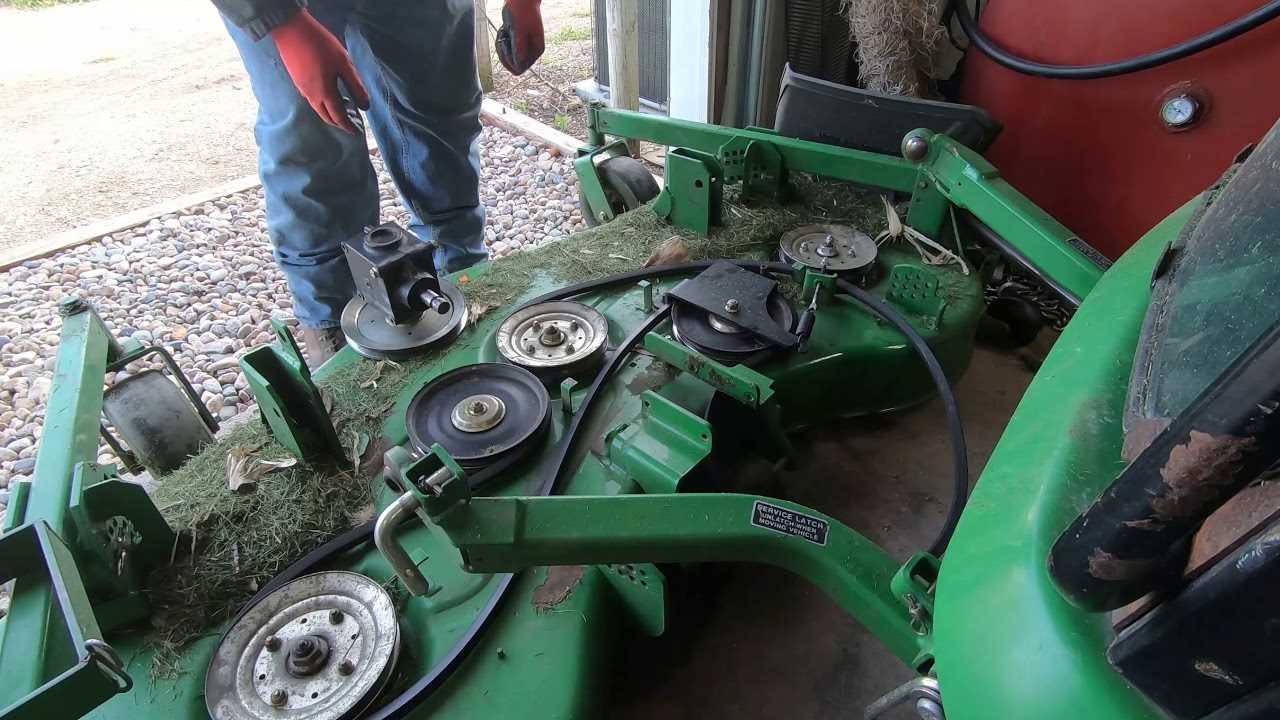
Another important feature is the adjustable height control. This flexibility lets the operator choose the ideal cutting level, depending on the condition and type of the grass. Additionally, the precision of the blades ensures even trimming, leaving a well-maintained and professional appearance after each pass.
Understanding the Belt System Layout
The belt arrangement in various machinery plays a crucial role in ensuring the smooth transfer of power across multiple components. A well-designed belt layout helps maintain efficiency by aligning different parts in an organized manner, which in turn ensures optimal performance. By understanding how the belts are positioned and the flow of movement, it becomes easier to diagnose issues and carry out maintenance.
Key Components of the Belt Arrangement
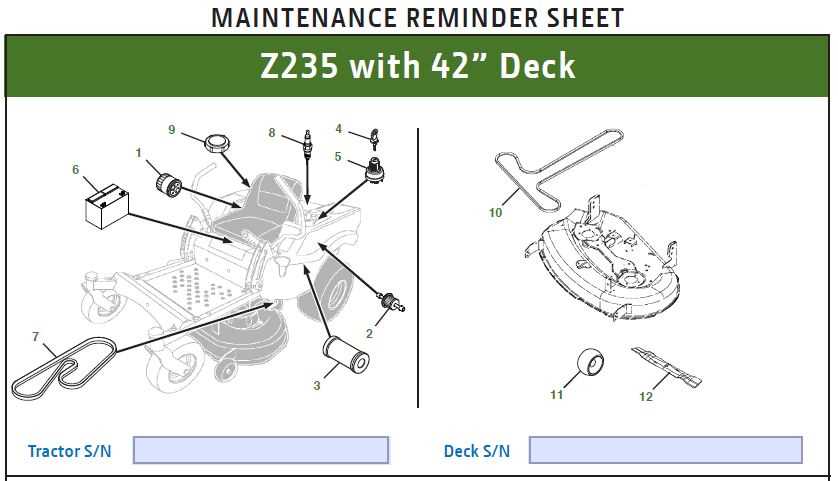
A typical belt system consists of several pulleys, tensioners, and belts that work together to transmit power. The pulleys are often mounted on rotating shafts, and the belts connect these pulleys, creating a closed loop that transfers energy. Tensioners are vital as they keep the belts tight, preventing slippage and ensuring co
Blade Configuration and Maintenance Tips
Proper setup and regular upkeep of cutting blades are essential for ensuring optimal performance and durability. A well-arranged cutting system allows for efficient grass trimming, while extending the lifespan of the blades. Understanding how to position blades correctly and knowing the best practices for their care are key elements to maintaining smooth operation over time.
When arranging blades, make sure they are aligned to maximize coverage and reduce strain on the machine. It’s also important to balance the blades evenly to avoid vibrations that could lead to premature wear. Inspect the sharpness frequently, as dull edges can result in uneven cuts and cause unnecessary stress on the system.
Regular cleaning and sharpening are vital steps in maintaining blade efficiency. After every use, remove debris and inspect for any signs of damage, such as cracks or bent sections. Sharpen the edges as needed to keep them at peak performance, and replace worn blades to prevent further damage to the machine.
Exploring the Spindle Assembly Design
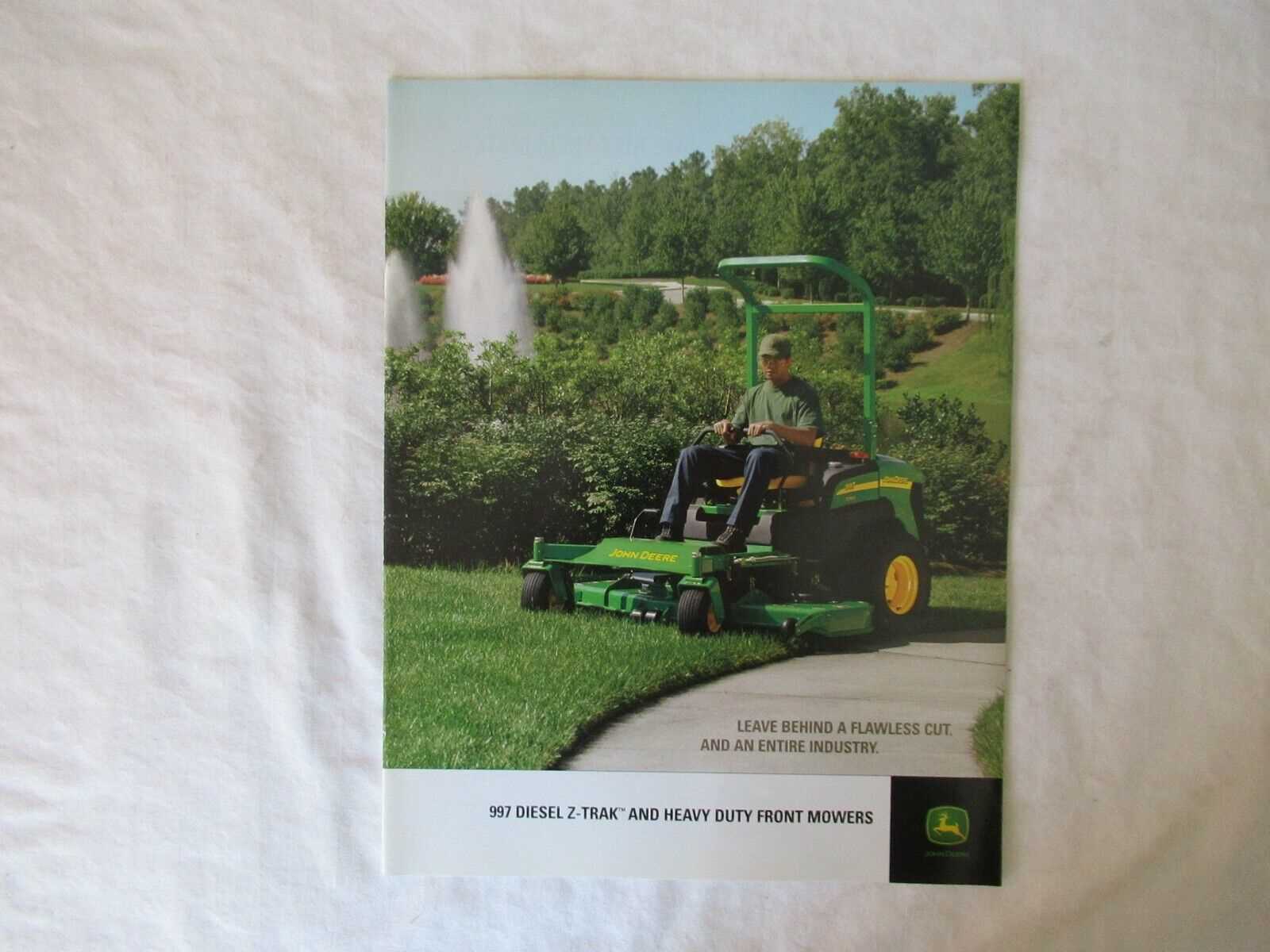
The spindle assembly plays a crucial role in the operation of mechanical cutting systems. It ensures that rotational power is transferred effectively, allowing the blades to perform their task efficiently. Understanding the design of this assembly helps in maintaining the device’s performance, reducing wear, and ensuring longevity.
- Core Structure: The spindle consists of several key components that work together to maintain stability and smooth rotation.
- Bearings: Positioned to support the shaft, these reduce friction, ensuring the rotating parts move effortlessly and with minimal resistance.
- Housing: The outer casing provides protection from external debris while also offering structural support to the entire unit.
Regular inspection and proper lubrication are essential to ensure the spindle assembly remains in good condition,
Role of the PTO Shaft in Operation
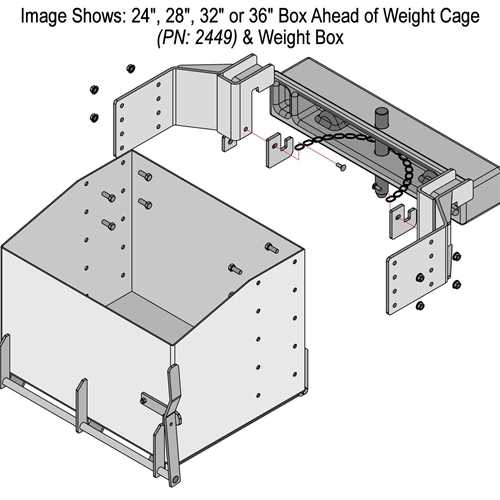
The Power Take-Off (PTO) shaft is a vital component in transferring energy from a machine’s engine to the attached equipment. Its primary function is to deliver mechanical power, ensuring that various attachments operate efficiently. This transmission of force allows multiple tools to work in sync with the main engine, improving productivity and reducing the need for separate power sources.
Energy Transfer and Efficiency
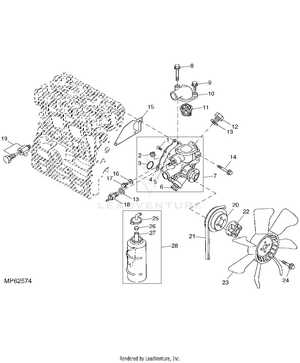
The PTO shaft connects the power source to the implement, creating a direct energy transfer. This setup eliminates the need for independent motors, maximizing energy efficiency. The consistent flow of mechanical energy helps maintain stable operation, ensuring the attachment performs as expected under varying conditions.
- Seamless connection between engine and attachment
- Efficient use of the engine’s power output
- Identifying Common Wear Parts
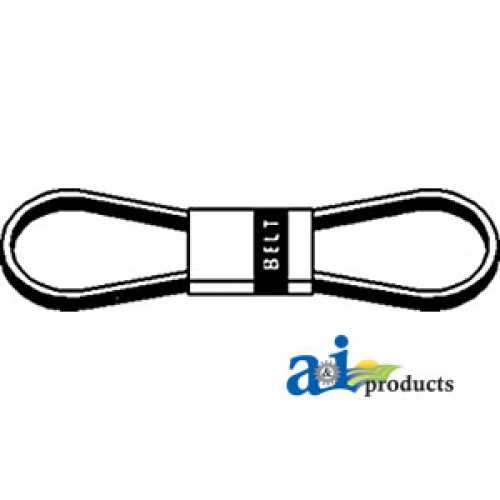
During regular use, certain components of equipment are more prone to deterioration due to constant movement, friction, and exposure to various elements. Understanding which parts are most likely to experience wear can help in maintaining optimal functionality and reducing unexpected downtime. This section highlights the most frequently affected areas and provides an overview of their typical wear indicators.
Component |
Wear Indicator |
Suggested Action |
Blades |
Dull edges, uneven cutting |
Sharpen or replace |
Belts |
Cracks, fraying |
Replace |
Bearings |
Noisy operation, vibration |
Deck Housing Structure and Protection
The structure of the housing for mowing equipment plays a crucial role in ensuring effective operation and longevity. This component not only houses essential elements but also provides a framework that supports various functionalities. The materials used in its construction contribute significantly to its durability and resistance to wear and tear from regular use.
Proper protection mechanisms are vital to prevent damage from external factors such as debris, moisture, and impacts. Reinforcements in strategic areas enhance resilience while maintaining lightweight characteristics. Additionally, incorporating features that facilitate easy maintenance can extend the lifespan of the housing, ensuring it remains functional over time.
Understanding the design and protective aspects of this assembly allows for better maintenance practices. Regular inspections and timely repairs can mitigate potential issues, enhancing performance and efficiency. By focusing on the integrity and protection of the housing, users can ensure optimal functionality of their equipment.
Connection Points for Hydraulic Systems
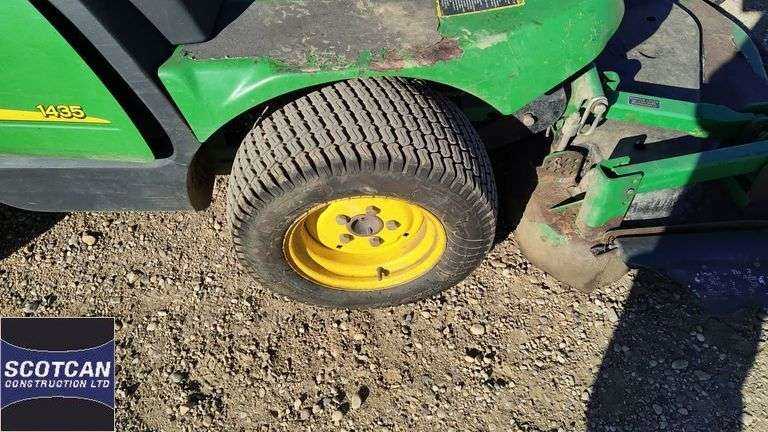
Understanding the various connection points within hydraulic systems is essential for optimal performance and maintenance. These points facilitate the transfer of fluid, enabling efficient operation of machinery. Proper identification and management of these connections ensure smooth functionality and help in troubleshooting issues that may arise during usage.
- Hydraulic Hoses: These flexible tubes are crucial for transporting hydraulic fluid between components. Regular inspection for wear or damage is vital.
- Fittings: Various types of fittings, such as elbows, tees, and connectors, play a significant role in joining hoses and pipes, ensuring a secure and leak-free connection.
- Valves: These control the flow of hydraulic fluid. They can be manually operated or electronically controlled, affecting the overall efficiency of the system.
- Actuators: Often positioned at the end of the hydraulic lines, these devices convert hydraulic energy into mechanical movement, playing a key role in the machine’s operation.
- Reservoirs: These storage tanks hold hydraulic fluid, allowing for the system’s fluid to be replenished and maintaining pressure.
Regular maintenance and monitoring of these connection points are critical for ensuring the longevity and efficiency of hydraulic systems. Proper lubrication, timely replacement of worn components, and adherence to recommended operating procedures can significantly enhance performance.
Steps for Replacing the Idler Pulley
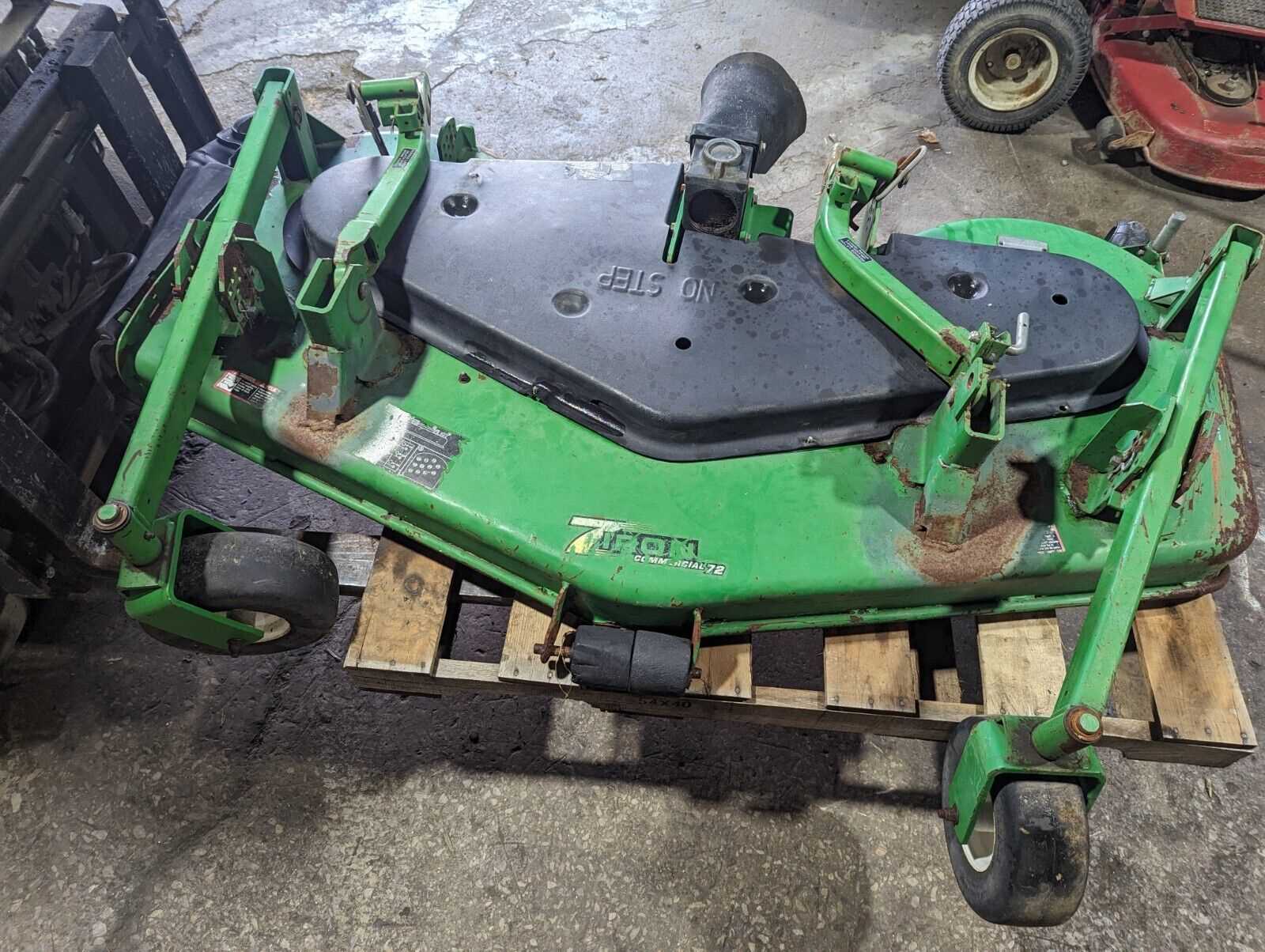
Replacing the idler pulley is an essential maintenance task that helps ensure the efficient operation of the machine’s drive system. This procedure involves a series of straightforward steps that can be performed with basic tools and some attention to detail. By following the correct approach, you can restore optimal function and prevent further issues down the line.
Preparation for the Replacement
Begin by ensuring the machine is turned off and completely cool. Disconnect the power source to avoid any accidents during the replacement process. Gather the necessary tools, including wrenches and a replacement pulley, to facilitate a smooth workflow. It may also be helpful to consult the user manual for specific guidance related to your equipment.
Executing the Replacement
Locate the existing idler pulley and remove any covers or guards that may obstruct access. Carefully detach the old pulley by loosening the bolts or nuts securing it in place. Once removed, position the new idler pulley and secure it using the original hardware. Finally, reattach any covers or guards, and reconnect the power source to complete the process.
Troubleshooting Common Deck Issues

Maintaining a lawn care machine requires attention to various components that may encounter problems over time. Identifying and resolving these issues early can enhance performance and extend the lifespan of the equipment. This section aims to guide users through the common challenges faced by the mowing platform and provide practical solutions for effective management.
Identifying Unusual Noises
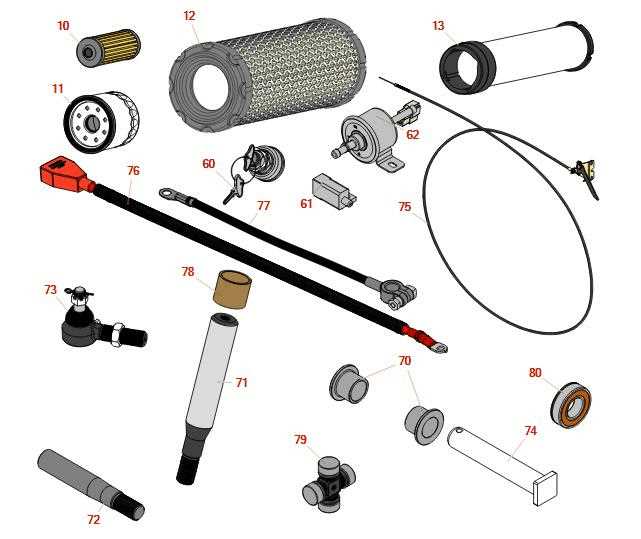
If the machinery produces unexpected sounds during operation, it could indicate loose or damaged components. First, inspect all moving parts for signs of wear or misalignment. Tighten any loose screws or bolts, and replace any worn-out components. Listening for specific sounds can also help pinpoint the source of the issue, allowing for more targeted repairs.
Uneven Cutting Performance
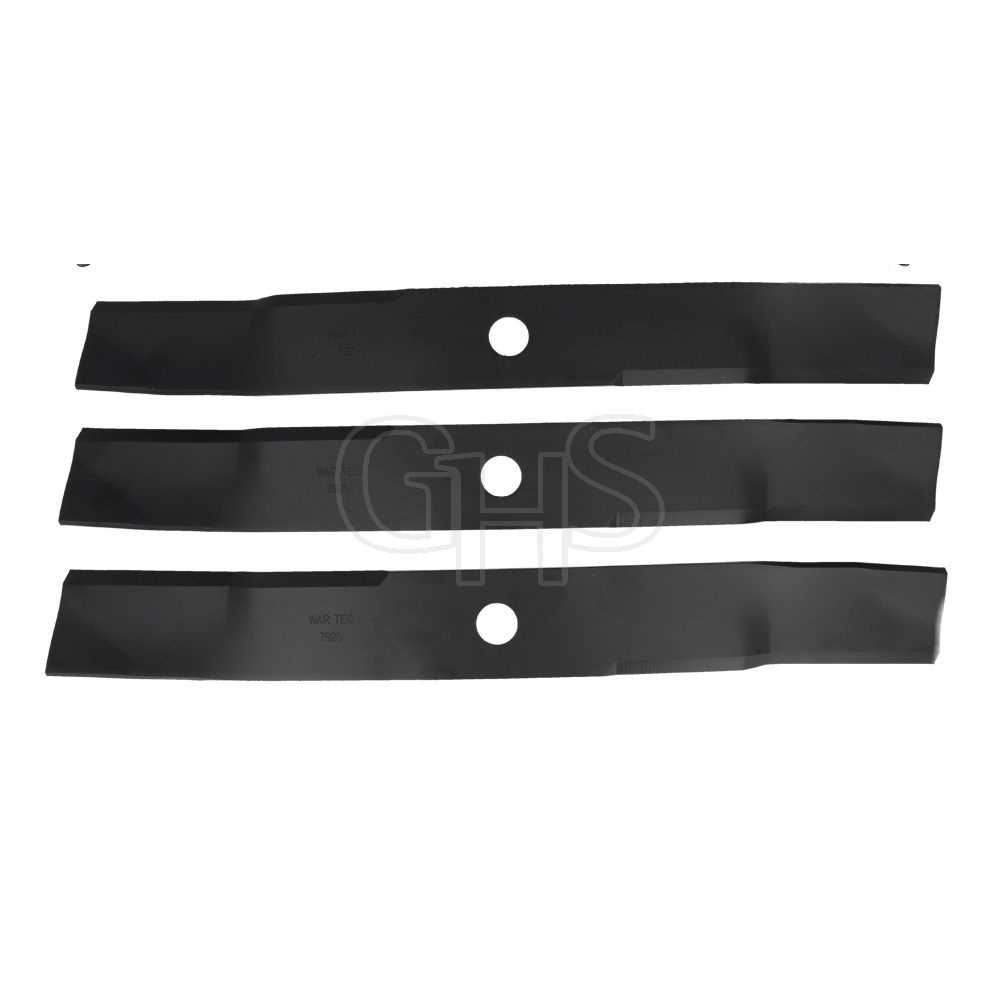
Inconsistent cutting results can be frustrating. This issue may arise from dull blades or improper height settings. Begin by examining the blades for sharpness and replacing them if necessary. Additionally, check the height adjustment settings to ensure they are set correctly for the type of grass being mowed. Regularly cleaning under the machine will also prevent clippings from accumulating and affecting performance.