Understanding the elements that make up the blade and spindle assembly is crucial for ensuring efficient performance and smooth operation. These interconnected parts work together to provide a clean, even cut and maintain the overall functionality of the cutting system. Proper knowledge of these components can help in maintenance and troubleshooting.
The blade is the primary cutting element, responsible for slicing through grass or vegetation. It is mounted to the spindle, which rotates the blade at high speeds. Blades vary in design and material, with some offering features like serrated edges for improved cutting performance.
The spindle plays a vital role in transferring power from the engine to the blade. It consists of a shaft and bearings housed within a spindle assembly, allowing for smooth rotation. Regular maintenance of the spindle bearings ensures longevity and optimal operation of the blade system.
Component |
Function |
Electrical System Parts and Connections
The electrical system of any machinery is crucial for its operation and efficiency. Understanding the various components and their interconnections helps ensure optimal performance and reliability. This section outlines the essential elements involved in the electrical setup, emphasizing their roles and relationships within the overall system.
Power Source: The heart of the electrical system, the power source, provides the necessary energy for operation. It can be in the form of batteries or generators, ensuring that all components receive adequate power.
Wiring Harness: A complex network of cables, the wiring harness facilitates communication and power distribution between different parts. Proper insulation and protection of these wires are vital to prevent shorts and ensure longevity.
Connectors: Connectors play a significant role in establishing secure links between various electrical components. They are designed to allow easy assembly and disassembly, aiding in maintenance and troubleshooting.
Switches: These devices control the flow of electricity, enabling or disabling various systems as needed. They come in different forms, such as toggle, push-button, and rotary, each serving specific functions within the electrical network.
Sensors: Sensors monitor various parameters within the machinery, providing real-time data to the control unit. This feedback is essential for adjusting operations and enhancing efficiency.
Control Module: The brain of the electrical system, the control module processes signals from sensors and commands other components accordingly. It ensures that the machinery operates smoothly and efficiently, responding to changes in conditions.
Understanding these elements and their interconnections is crucial for anyone working with machinery. Proper maintenance and knowledge of the electrical system can prevent issues and extend the equipment’s lifespan.
Drive System Components
The drive system of a high-performance lawn care machine is essential for ensuring optimal functionality and efficiency. It comprises various elements that work in harmony to facilitate movement and maneuverability, allowing operators to navigate diverse terrains effortlessly.
Key Elements of the Drive Mechanism
The drive mechanism includes critical components such as the transmission assembly, which is responsible for transferring power from the engine to the wheels. Additionally, the axle plays a vital role in supporting the weight of the machine while allowing for smooth rotation. Furthermore, the belts and pulleys work together to create the necessary tension and control speed, contributing to the overall performance of the equipment.
Importance of Regular Maintenance
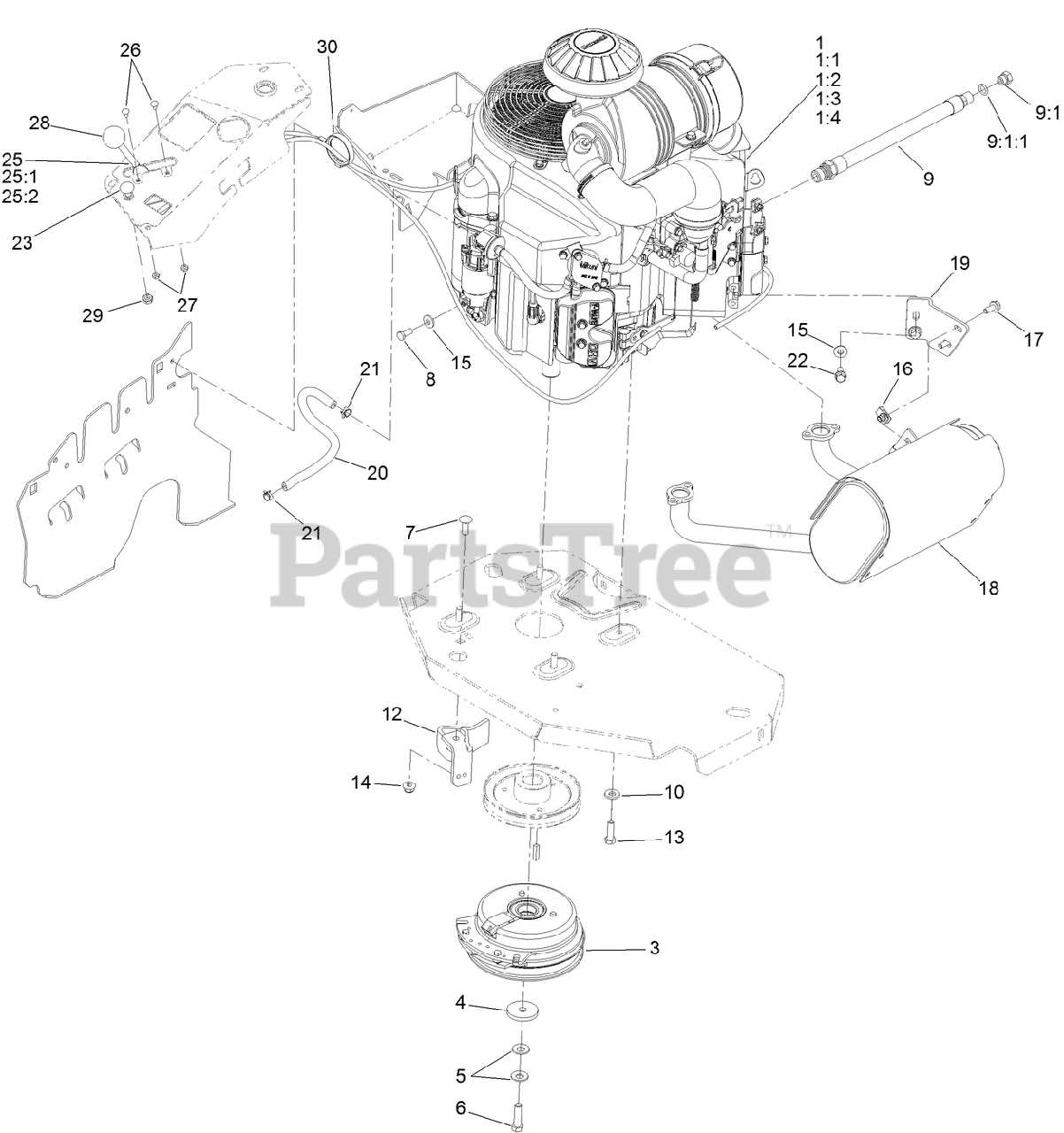
Regular inspection and maintenance of these components are crucial for ensuring longevity and reliability. Neglecting any part of the drive system can lead to decreased efficiency and potential failures. Routine checks and timely replacements can enhance performance and prolong the lifespan of the machinery.
Fuel System Overview and Critical Parts
The fuel system is an essential component in ensuring the efficient operation of any machinery. It is responsible for delivering the necessary fuel to the engine, where it is mixed with air and combusted to produce power. Understanding the key elements of this system is crucial for maintenance and troubleshooting, as any malfunction can significantly impact performance.
Key Components of the Fuel System
- Fuel Tank: The reservoir that stores fuel before it is fed into the engine.
- Fuel Pump: Responsible for transferring fuel from the tank to the engine, maintaining adequate pressure.
- Fuel Filter: Removes impurities and debris from the fuel to protect engine components.
- Fuel Lines: Tubes that transport fuel from the tank to the pump and then to the engine.
- Fuel Injectors: Atomize the fuel, allowing for a fine mist that mixes with air for combustion.
Importance of Regular Maintenance
Regular maintenance of the fuel system is vital for optimal performance. Routine checks can help identify potential issues such as leaks, blockages, or worn components. Ensuring that filters are clean and fuel is free from contaminants will not only enhance efficiency but also prolong the lifespan of the engine.
- Inspect fuel lines for cracks or leaks.
- Replace the fuel filter as recommended.
- Monitor fuel levels and quality regularly.
Detailed Diagram of the Steering System
The steering mechanism of a machine plays a crucial role in ensuring precise control and maneuverability. Understanding its components and how they interact is essential for effective maintenance and troubleshooting. This section provides a comprehensive overview of the steering system, highlighting its vital elements and their functions.
Components of the Steering Mechanism
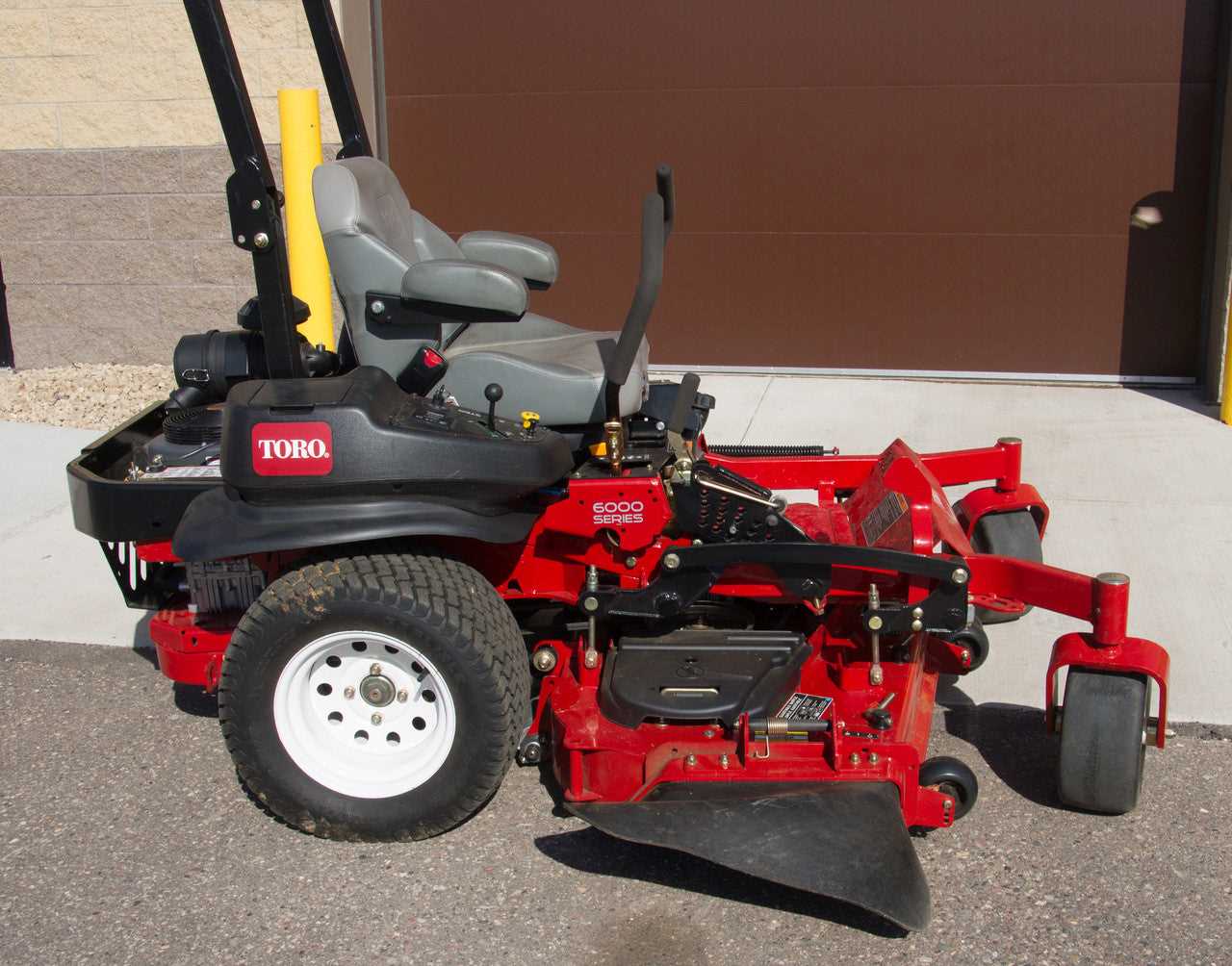
The steering system comprises various parts that work together to facilitate smooth navigation. Key components include the steering wheel, linkage rods, and the pivot points. Each element is designed to transmit motion effectively, allowing operators to steer with accuracy and ease.
Functionality of the Steering Assembly
At the core of the steering assembly is the mechanism that converts the rotational movement of the steering wheel into lateral movement of the wheels. This transformation is achieved through a series of linkages that connect the wheel to the axle, ensuring that the direction of travel aligns with the operator’s input. Proper alignment and maintenance of these components are essential for optimal performance.
Seat and Operator Control Mechanism
The operator’s seating and control system are crucial for achieving optimal performance and comfort during operation. This section delves into the essential components that enhance user experience, ensuring ease of handling and precise maneuverability. A well-designed control mechanism not only contributes to safety but also significantly impacts the efficiency of the equipment.
Ergonomic Design Features
Comfort is paramount when it comes to the seating arrangement for operators. An ergonomic design includes adjustable seating, providing support during extended use. Features such as cushioned seats, lumbar support, and easy-to-reach controls allow the operator to maintain focus on the task while minimizing fatigue.
Control Accessibility and Functionality
Accessibility of controls plays a vital role in the operational efficiency of the machinery. Controls should be intuitively placed, allowing for quick adjustments without compromising safety. The mechanism may include levers, pedals, and switches, all designed to facilitate a seamless interaction between the operator and the equipment.
Maintenance Essentials for Toro Z Master 3000 Parts
Proper upkeep is crucial for ensuring the longevity and efficiency of any outdoor equipment. Regular attention to essential components not only enhances performance but also minimizes the risk of breakdowns. Understanding the basic requirements for maintenance can lead to improved functionality and a smoother operation.
Routine Inspections: Conducting frequent checks on various elements is vital. Look for signs of wear and tear, loose connections, and any components that may require lubrication or tightening. Addressing minor issues promptly can prevent larger, more costly repairs down the line.
Cleaning and Care: Keeping the machinery clean is essential for optimal performance. Remove debris, grass clippings, and dirt that may accumulate around moving parts. A clean machine not only functions better but also reduces the risk of rust and corrosion.
Lubrication: Regularly lubricate moving parts to ensure smooth operation. This helps to reduce friction and wear, ultimately extending the life of the machinery. Refer to the manufacturer’s guidelines for specific lubrication points and recommended products.
Replacement of Worn Components: Over time, certain elements will naturally wear out and require replacement. Staying proactive about identifying these components can save time and money. Keep a close eye on belts, blades, and filters, replacing them as necessary to maintain peak performance.