The mechanism responsible for the advancement and release of the cutting line plays a crucial role in the efficient operation of trimmers and brush cutters. This system ensures that the line is dispensed correctly during use, allowing for optimal cutting performance without the need for frequent manual adjustments.
Typically, this setup includes a spool that holds the line securely while allowing it to extend as needed. When the user activates the tool, centrifugal force engages the release mechanism, enabling the line to feed out smoothly. This design not only enhances convenience but also improves overall productivity, making it easier to maintain a clean and precise cutting line.
Furthermore, many modern implementations feature automatic feed systems that sense when the line is getting short and adjust the release accordingly. This innovation minimizes downtime and ensures that the user can focus on the task at hand without interruptions. Overall, an efficient line feed and release system is essential for achieving optimal results in various landscaping tasks.
The locking mechanism in this cutting tool plays a crucial role in ensuring safe and effective operation. It is designed to secure various components in place during use, preventing accidental disassembly and enhancing the overall reliability of the device. Understanding how this system functions can significantly improve the user experience and maintenance procedures.
This mechanism typically consists of a series of interlocking parts that engage when the tool is assembled. When the user initiates operation, the locking system ensures that all components remain firmly connected, even under stress. This stability is vital for achieving optimal cutting performance and reducing the risk of malfunction.
Wear and Tear Prevention Parts
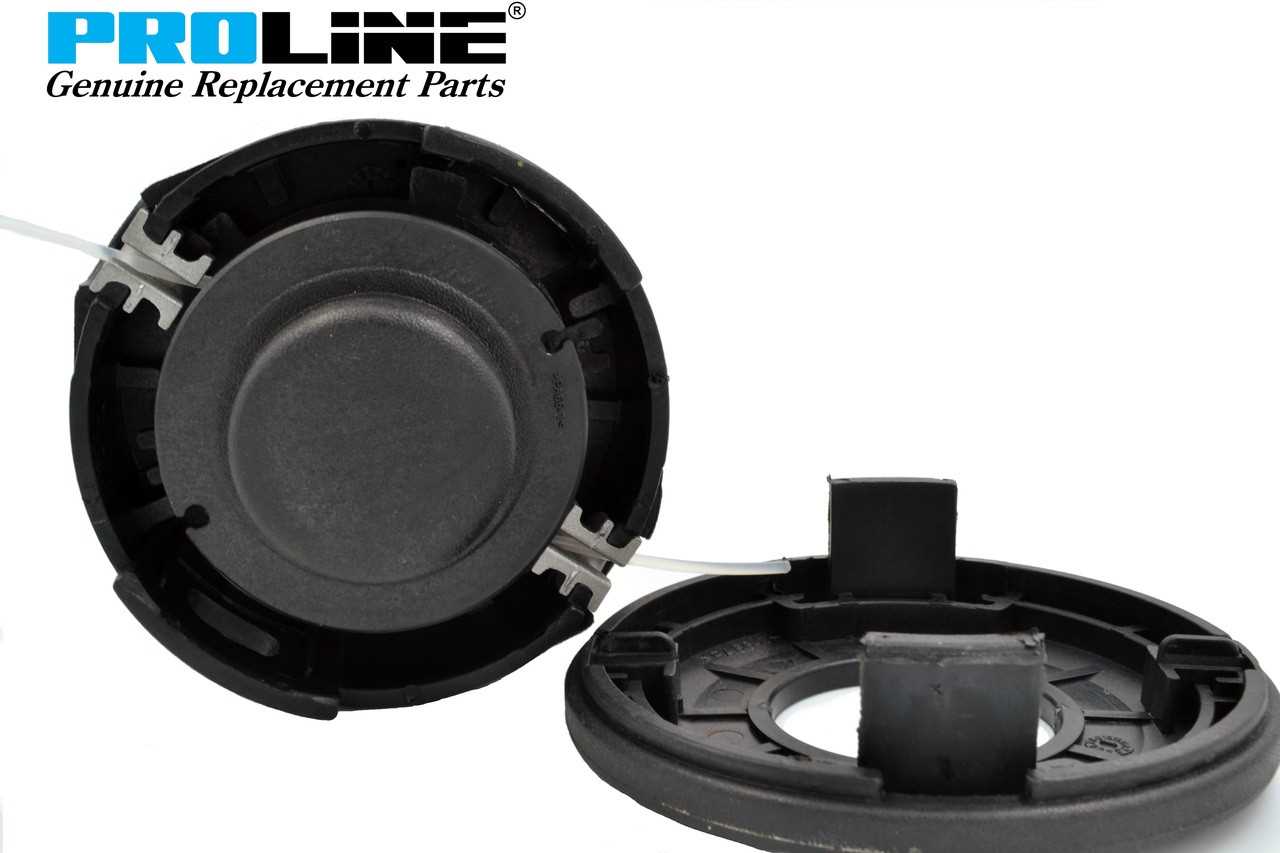
Maintaining optimal performance and extending the lifespan of your equipment requires careful attention to various components designed to minimize deterioration. Implementing preventive measures can significantly reduce the likelihood of breakdowns and ensure seamless operation during use.
To achieve longevity and efficiency, consider focusing on the following elements:
- High-Quality Blades: Opt for blades that are designed to withstand prolonged usage while maintaining sharpness.
- Durable Trimmer Heads: Select heads that offer robust construction to resist impact and wear over time.
- Reinforced Cables: Use cables made from strong materials to prevent fraying and damage during operation.
- Protective Guards: Equip your device with guards that shield sensitive areas from debris and impacts.
Regular inspections and timely replacements of these components play a crucial role in maintaining functionality and preventing unexpected failures. Keeping an eye on wear indicators will allow for proactive management and timely intervention.
Line Holder and Compatibility
The line holder is a crucial component that significantly influences the efficiency of cutting tasks. It is designed to securely accommodate the trimmer line, ensuring optimal performance while maintaining ease of use. Understanding the compatibility of this part with various models is essential for users seeking to maximize their equipment’s effectiveness.
Key Features of the Line Holder
- Durability: Constructed from robust materials to withstand wear and tear.
- Easy Installation: Designed for straightforward attachment and removal.
- Adjustable: Accommodates different line sizes for versatile cutting options.
Compatibility Considerations
When selecting a line holder, it is vital to consider the specific model of the trimming device. Here are some compatibility factors:
- Model Specifications: Always refer to the manufacturer’s guidelines for the recommended holder.
- Line Thickness: Ensure the holder can handle the line diameter for efficient cutting.
- Attachment Mechanism: Verify that the attachment method aligns with the equipment design.
Choosing the right line holder not only enhances cutting efficiency but also extends the lifespan of the trimming tool.
Mounting Instructions for the Head
Proper assembly of the cutting head is essential for optimal performance and safety during operation. This section outlines the necessary steps to securely attach the head to your device, ensuring it functions efficiently while minimizing the risk of accidents.
Begin by gathering all required components, including the head assembly and mounting accessories. Make sure the device is powered off and disconnected from any power source to prevent accidental starts. Carefully align the mounting holes of the head with the corresponding fittings on the device.
Next, insert the fasteners through the holes and tighten them securely using the appropriate tools. Ensure that the head is firmly attached and does not exhibit any play or movement. It’s important to follow the manufacturer’s guidelines regarding torque specifications to avoid damaging components.
After securing the head, perform a visual inspection to confirm that everything is in place. Before operating, conduct a brief test to check for stability and proper function. This preventive step can help identify any potential issues before beginning work.
Maintenance and Cleaning Procedures
Regular upkeep and thorough cleaning are essential for ensuring the longevity and optimal performance of your cutting tool. These practices not only enhance efficiency but also contribute to safety during operation. By adhering to systematic procedures, you can minimize wear and prevent potential malfunctions.
Routine Maintenance Steps
Establishing a consistent maintenance schedule is vital. Begin by inspecting the equipment for any signs of wear or damage. Pay close attention to the cutting line and housing, as these components are subject to frequent stress. Lubricate moving parts as recommended, ensuring that they operate smoothly. Additionally, replace worn-out components promptly to maintain peak performance.
Cleaning Techniques
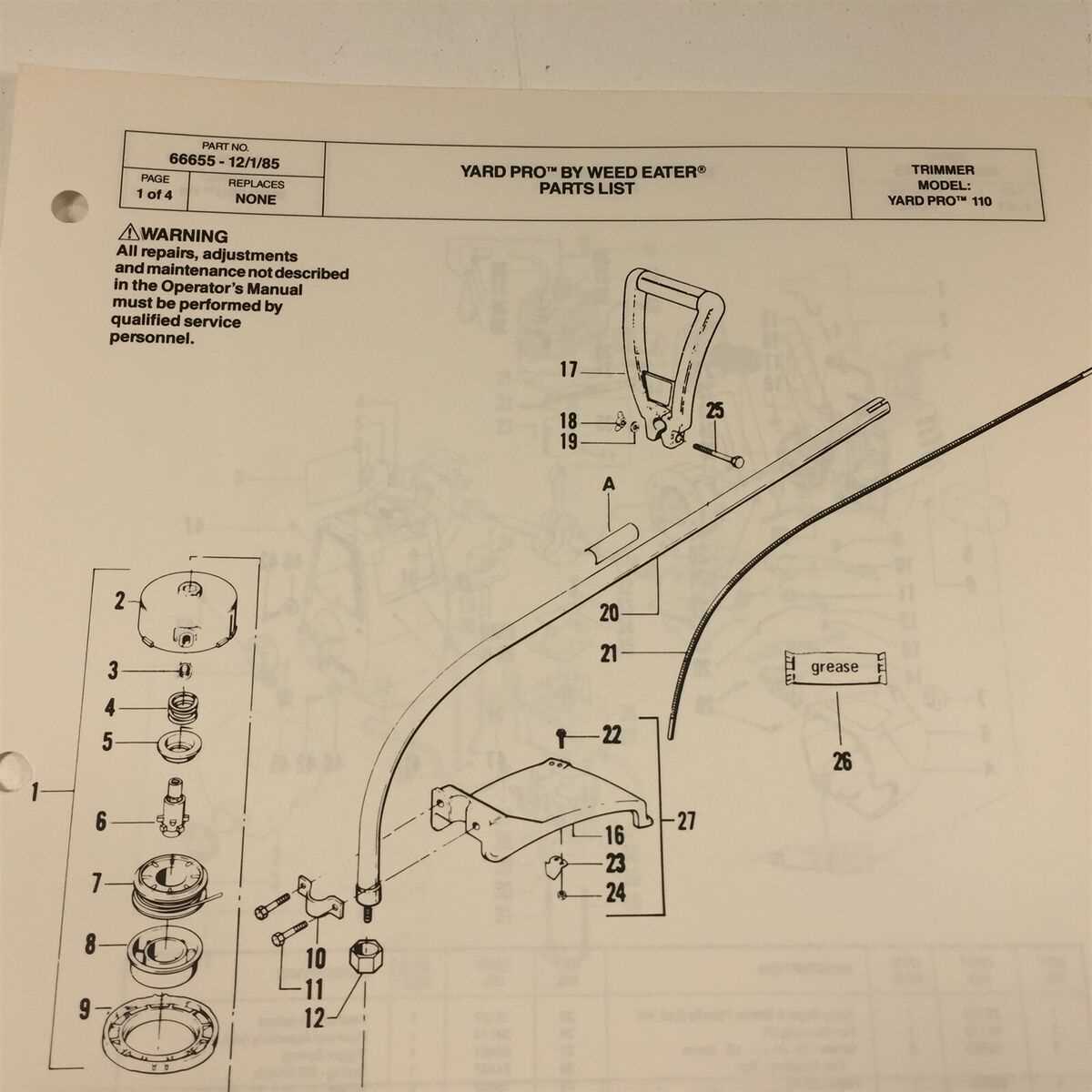
After each use, clean the equipment to remove debris and dirt that can accumulate during operation. Use a soft brush or cloth to wipe down the exterior and prevent buildup that could hinder functionality. For stubborn residues, a mild detergent mixed with water can be used. Ensure all parts are completely dry before storage to prevent rust and corrosion. Regularly check and clear any blockages in the line feed system to maintain efficient operation.
Troubleshooting Common Issues
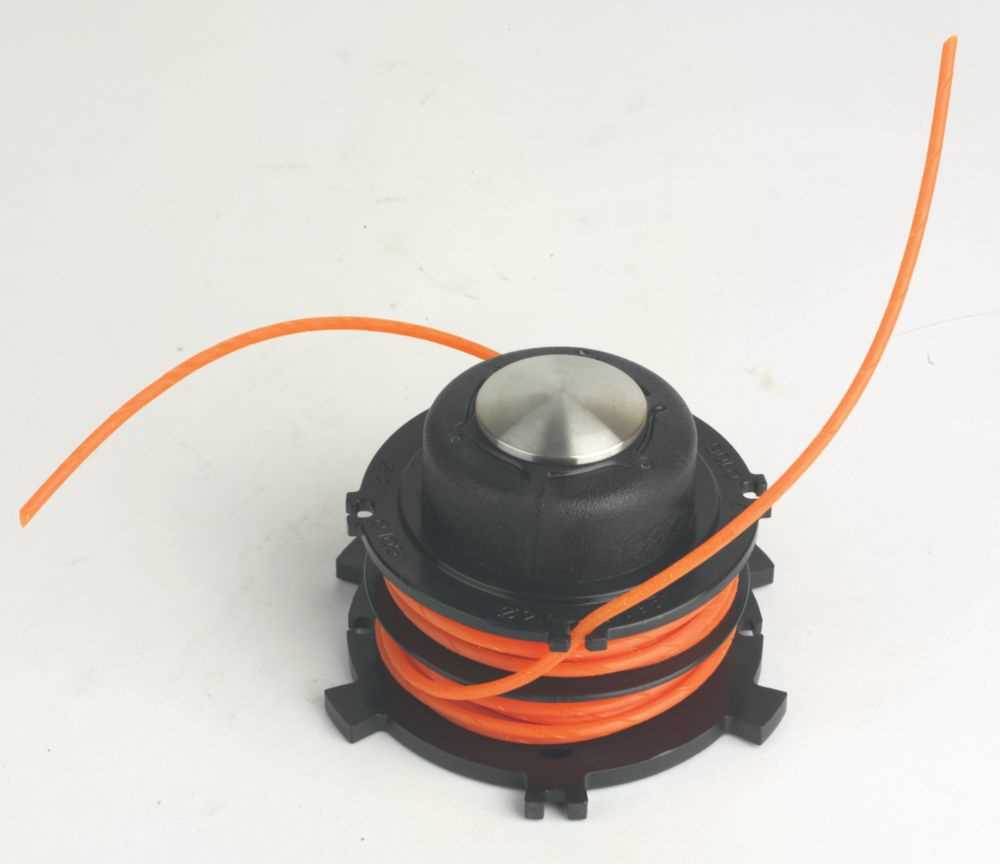
When operating cutting equipment, various challenges may arise that can hinder performance. Understanding the common problems and their solutions can enhance efficiency and prolong the lifespan of the device. This section outlines typical issues and practical steps for addressing them.
-
Difficulty Starting:
If the equipment fails to start, check the fuel supply and ensure that the ignition system is functioning correctly. Inspect the air filter for blockages and clean or replace it if necessary.
-
Uneven Cutting:
When the tool produces uneven cuts, verify that the cutting line is properly installed and tensioned. Additionally, inspect the cutting head for wear or damage.
-
Excessive Vibration:
Excessive vibrations can indicate an imbalance in the cutting assembly. Check for debris accumulation and ensure that all components are securely fastened.
-
Overheating:
If overheating occurs, allow the equipment to cool down and inspect for any blockages in the cooling system. Ensure that the device is not being overloaded during operation.
-
Frequent Line Breakage:
Frequent breakage of the cutting line may result from improper winding or using low-quality materials. Ensure that the line is wound correctly and consider switching to a more durable option.
By systematically addressing these common issues, users can maintain optimal functionality and achieve better results with their cutting tools.